Case Study: How Lean Green Belt Training Transformed Quickslide's Operations
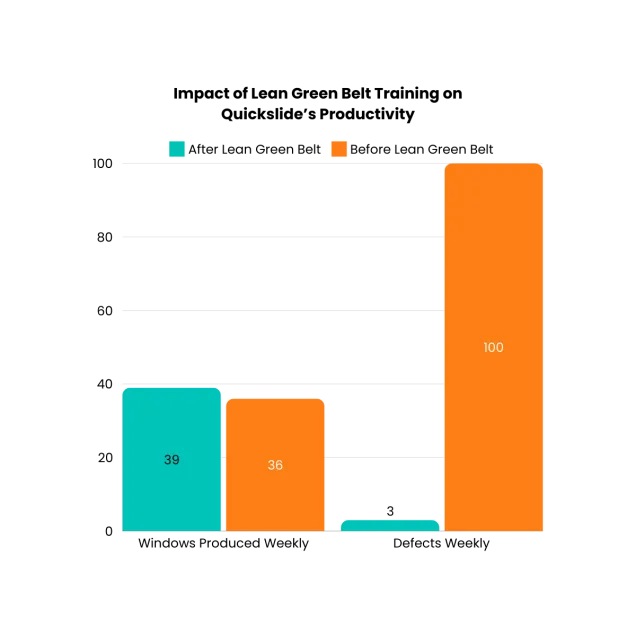
Background
Quickslide operates from a state-of-the-art facility in Brighouse, specializing in uPVC sash sliding windows with over 1 trillion possible configurations. The business was established to preserve the period look of windows while improving insulation and maintenance, addressing a gap in the market. Over the years, Quickslide has expanded by bringing many supporting processes in-house to control lead times and quality.
Despite its growth, the business faced challenges such as:
- Low operational team engagement.
- High defect levels, rework, and waste.
- Operator downtime.
- Inefficiencies in introducing new products.
To address these, Production Manager Lyndon and colleagues attended the Lean Green Belt Training to understand and improve existing manufacturing processes.
Course Overview
- Duration: 5 days, delivered in two blocks over 4-6 weeks.
- Content:
- Days 1-3 introduced lean productivity principles and techniques using the DMAIC model (Define, Measure, Analyze, Improve, Control).
- Days 4-5 refined project details and quantified outputs.
- Focus: Practical exercises and tools for productivity challenges.
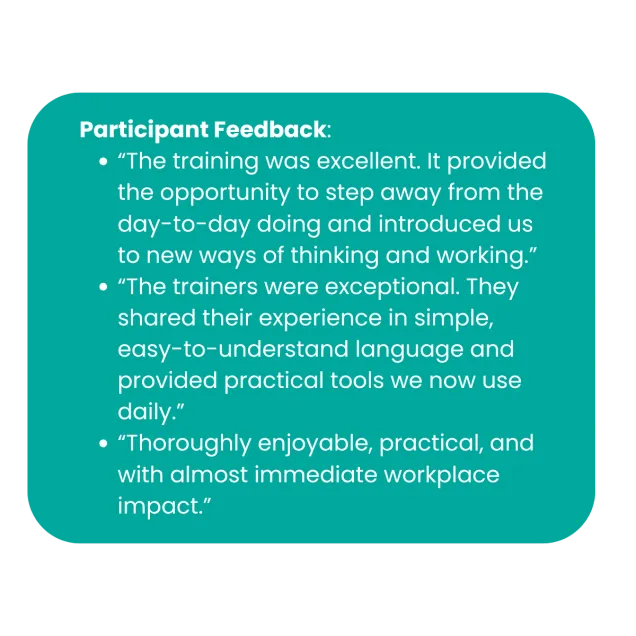
Approach and Implementation
After completing the training, Quickslide implemented several initiatives, including:
- A1 Reporting
- Introduced communication boards and simple forms to document challenges and solutions collaboratively.
- Outcome: Structured information sharing facilitated continuous improvement.
- Observation Stations
- Supervisors observed key locations, documented findings, and used insights for improvement.
- Outcome: Identified small opportunities that enhanced output.
- Workstation Call Points
- Installed touchscreens at workstations for quick issue reporting.
- Outcome: Reduced downtime, enabling more consistent target achievement.
- Housekeeping (5S)
- Implemented 5S methodologies, shadow boards, painted floor markings, and purpose-built workbenches.
- Outcome: Improved organization and set clear expectations through visuals and posters.
These are just a few examples of the many initiatives adopted that are contributing to enhanced productivity, and a culture of continuous development.
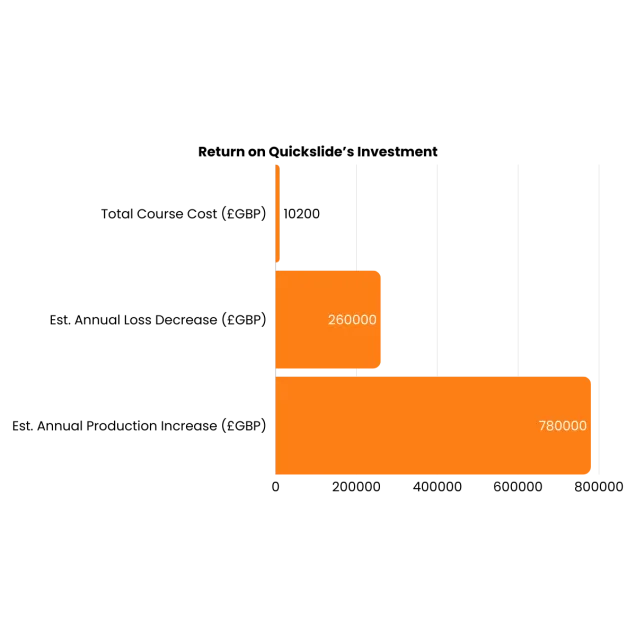
Outcome and Results
- Defect Reduction:
- Reduced defects from 100 to 3 per week.
- Financial Value: £5,000 saved weekly.
- Productivity Increase:
- Purpose-built workbenches boosted production from 36 to 39 windows per week.
- Financial Value: £15,000 added weekly.
- Improved Engagement:
- Enhanced communication and involvement in continuous improvement initiatives.
- “Our production team is more engaged and communicates better than ever before.”
Key Takeaways
- Practical training can yield immediate workplace impact.
- Small, consistent gains contribute to substantial organizational improvement.
- Engaging teams in continuous improvement fosters a culture of collaboration.
- “The tools provided during training are now part of our daily operations and have transformed how we approach challenges.”
- All participants are now certified
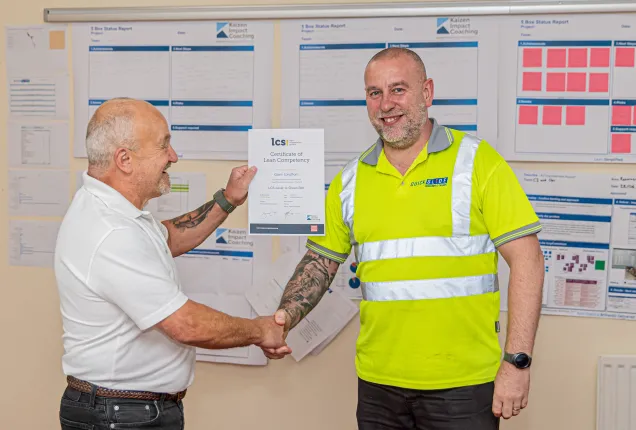
Conclusion
Quickslide’s journey through Lean Green Belt Training underscores the transformative potential of targeted skill development in addressing operational inefficiencies. By implementing practical tools and fostering a culture of continuous improvement, Quickslide achieved notable reductions in defect rates and enhanced productivity. Beyond financial gains, one of the most profound outcomes was the improvement in team engagement and communication, which has bolstered morale and fostered a collaborative workplace environment.
The success experienced by Quickslide highlights the value of structured training programs like Lean Green Belt Training. Which is why West Yorkshire Manufacturing Services provides these courses to organisations facing similar challenges, investing in such initiatives can lead to measurable results and sustained improvements on a large scale, contributing to continuous improvement and innovation in the manufacturing industry as a whole.